Failing to meet MSHA’s silica standards can cost more than fines—it can disrupt operations, hurt worker morale, and damage your mine’s reputation. Overexposures often occur because it’s difficult to pinpoint the root cause without accurate, timely data, leaving safety teams guessing.
The quality of silica exposure data determines how effectively a site can respond to risks. Poor data—whether delayed, incomplete, or non-actionable—creates hidden costs that add up quickly. Here’s how better data can prevent costly mistakes and protect your operation.
Learn more about real-time monitoring for MSHA silica compliance.
The hidden costs of poor data
When a mine relies exclusively on lab-based (gravimetric) sampling for silica exposure data, two critical issues often arise:
- Slow turnaround times: It usually takes 2–4 weeks between sampling workers and receiving lab results.
- Limited insights: Lab-based sampling provides a shift-average exposure number, which is useful for compliance but rarely actionable for identifying the root cause of overexposures.
These limitations often lead to costly outcomes:
1. Investing in the wrong controls
Without clear data, decision-makers typically err on the side of caution and implement expensive engineering controls, such as advanced ventilation systems or misting stations.
In many cases, simpler adjustments—like changing sweeping methods, reducing compressed air usage, or modifying workflows—could more effectively address the issue. Over-investing in unnecessary controls wastes time and resources that could have been better allocated.
2. Not acting at all
When safety and company leadership lack confidence in their data, they may delay decisions, opting to “wait and see.” This inaction increases exposure risks, leading to:
- Financial penalties from MSHA audits and potential disruption of operations
- Legal liabilities if workers experience silica-related illnesses.
- Rising medical expenses for affected employees.
Every delay compounds the cost of compliance and jeopardizes worker safety.
3. Operational and reputational damage
Overexposure incidents can trigger production downtime for investigations, increased scrutiny from regulators, and loss of trust among employees and neighboring communities.
A mine labelled as unsafe risks higher worker turnover, reduced productivity, and difficulty maintaining good standing with community stakeholders.
How real-time monitoring solves these problems
Real-time air quality monitoring addresses the core issues caused by poor silica exposure data, enabling mines to make more informed decisions and avoid unnecessary costs.
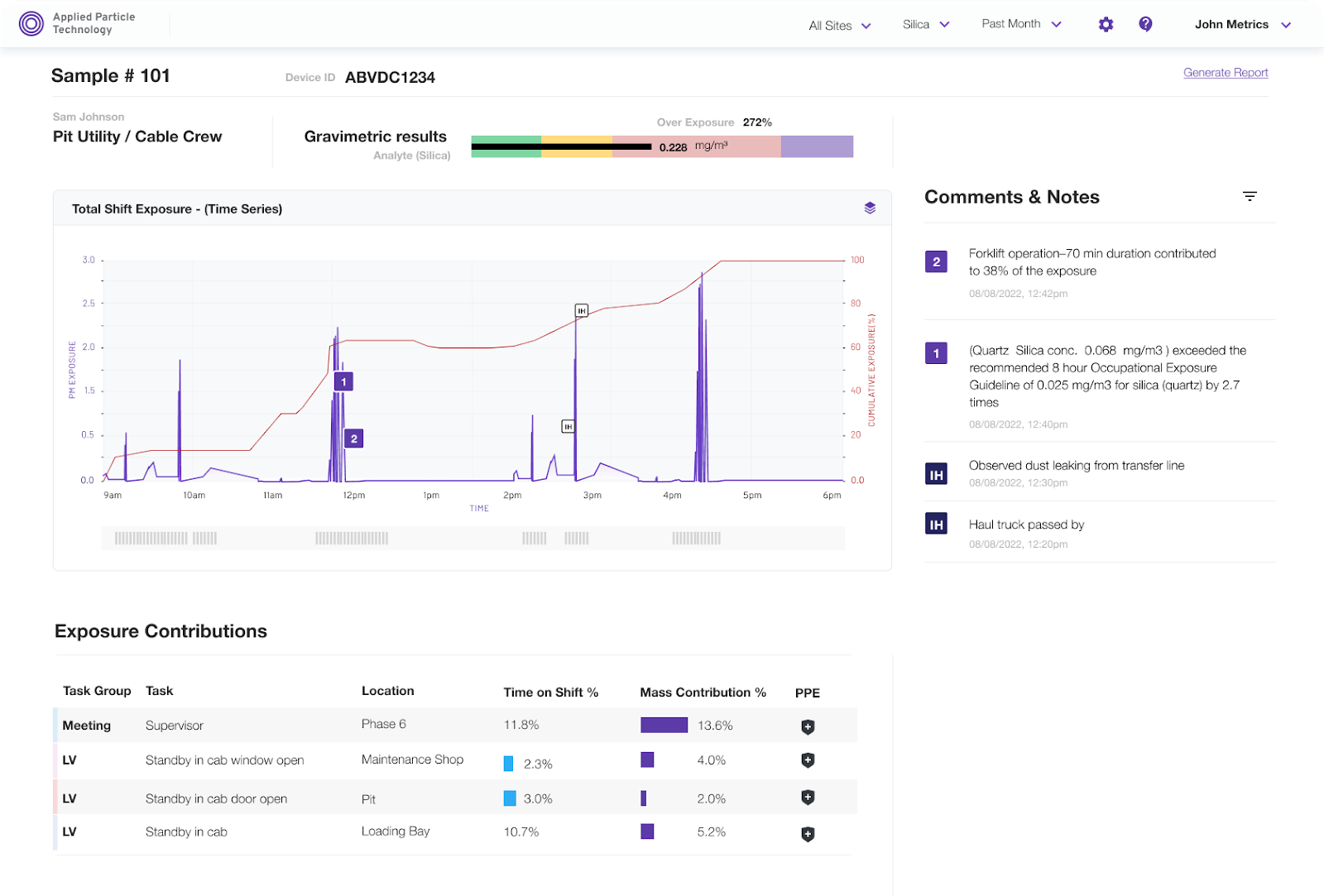
1. Quickly implementing effective controls
Real-time monitoring provides precise exposure data, allowing safety teams to identify the root cause of overexposures and evaluate potential solutions. Instead of over-engineering with costly site-wide controls like misting stations or advanced ventilation systems, teams can determine whether more minor adjustments—such as optimizing sweeping practices or reducing compressed air usage—might achieve the same result.
2. Making efficient, confident decisions
With reliable data about the source of silica exposure, teams can act with confidence, knowing that their proposed solution will result in lower exposures. This can reduce the cost of engineering controls and help safety & health teams back their decisions with data.
3. Minimizing operational and reputational damage
Real-time data helps mines avoid production downtime and reputational fallout by enabling faster root-cause analysis. Using time-stamped data and, if necessary, bodycam footage, teams can identify the specific activity or location responsible for overexposure events. This data speeds up corrective action and demonstrates a commitment to safety, maintaining trust with workers and the community while running operations smoothly.
The bottom line
Poor silica exposure data doesn’t just delay decisions—it can lead to overengineering, inaction, and compounding costs. Real-time air quality monitoring provides the actionable insights safety teams need to make faster, more confident decisions that protect workers and keep operations running smoothly.
If your mine is still relying on slow lab-based sampling alone, consider how real-time monitoring can reduce costs and simplify compliance. Ready to learn more?
Contact us or get an estimate to explore how real-time monitoring can fit into your compliance strategy.
Take a tour of APT's dust management platform
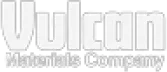
Vulcan Materials Company is the nation’s largest producer of construction aggregates.

Project partner
Brent Leclerc | Environmental Manager
Problems solved
Unjustified community dust complaints & lawsuits
Difficulty complying with opacity regulations and risk of NOVs
Solution
Real-time dust monitoring
Dust maps proving no community impact, preventing fines & lawsuits
Real-time opacity monitoring, high degree of compliance
Better decisions start with real-time insight
APT helps industrial teams move faster, act smarter, and stay compliant—because when you can see the problem clearly, you can solve it confidently.